Triple-Station Positive/Negative Pressure Thermoforming Machine
Positive and negative pressure three-station thermoforming blister machine is widely used in packaging, electronics, food, medicine and other industries due to its high efficiency, precision and automation. It not only improves production efficiency and saves space, but also ensures high quality and consistency of products.
Brif Intro
Positive and negative pressure three-station thermoforming blister machine is a high-efficiency equipment widely used in the fields of plastic packaging, plastic molding, etc. It is particularly suitable for the production of various plastic products, such as cosmetic packaging boxes, electronic product packaging, food trays, etc.
The characteristics of this equipment are that it can use both positive and negative pressure forces for thermoforming, and it has a three-station design, which can achieve more efficient and more precise production. This equipment is particularly suitable for mass production and complex shape molding needs.
Features of thermoforming machine
Advantages of thermoforming machines
Due to the three-station design, multiple process steps can be carried out simultaneously during the production process, reducing waiting and conversion time, thereby greatly improving production efficiency. The independent operation of each station ensures the continuity of the operation.
The equipment adopts positive and negative pressure molding technology, which can ensure the precise fit of plastic sheets in the mold, not only improving the molding accuracy of the product, but also ensuring the consistency of the product, especially suitable for the molding of complex shapes.
Because the three-station design integrates multiple work processes, it can save space and improve the efficiency of the production line. To a certain extent, it reduces equipment investment and site occupation, and reduces production costs.
The equipment can adapt to the thermoforming of a variety of plastic materials, such as PS, PET, PVC, PP, etc., so it can be widely used in packaging, electronics, automobiles, medical and other industries.
The positive and negative pressure molding system effectively reduces the waste of heat, and can quickly and evenly heat the plastic sheet, save energy, and improve the overall efficiency of the equipment, which meets the requirements of modern industry for environmental protection and energy saving.
Application of thermoforming machine
Cosmetic packaging
The positive and negative pressure three-station thermoforming blister machine is widely used in the cosmetic packaging industry, and can accurately produce various complex shapes of packaging boxes, bottle trays, mask packaging, etc. These packages not only have high transparency and beautiful appearance, but also can effectively protect the safety of cosmetics during transportation and use.
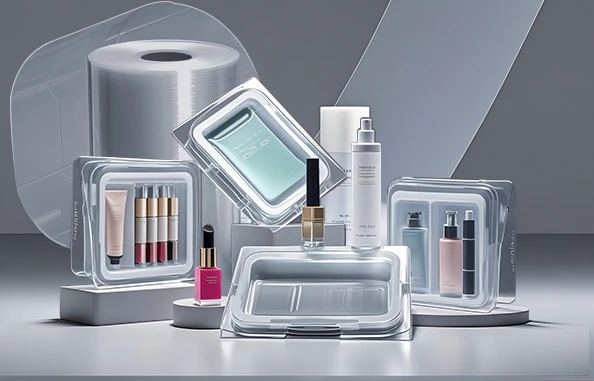
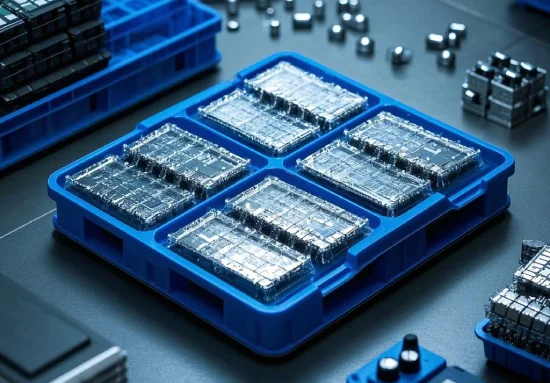
Electronic product packaging
The equipment can produce packaging boxes suitable for electronic components, mobile phone accessories, precision instruments, etc., provide shock-resistant, dust-proof, and anti-static packaging solutions, and protect electronic products from damage by the external environment.
Food packaging
In the food industry, positive and negative pressure three-station thermoforming blister machines are widely used in the production of various food trays, fresh-keeping packaging boxes, fruit and vegetable boxes, etc., which can ensure the sealing and hygiene of the packaging, and at the same time have good air permeability to extend the shelf life of food.
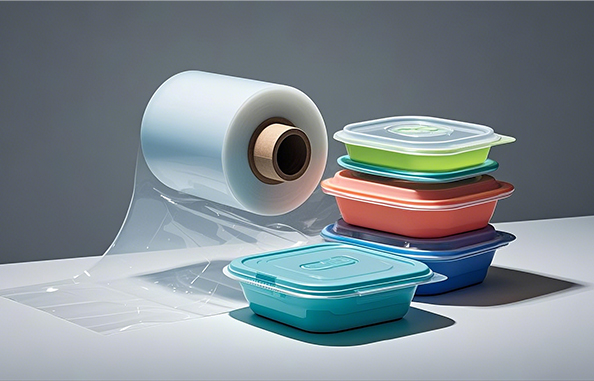
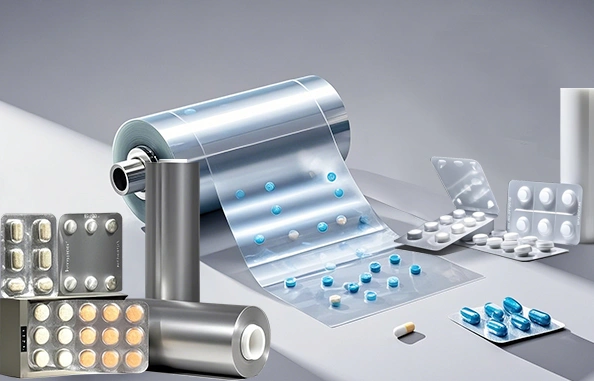
Pharmaceutical packaging
The equipment can be used to produce pharmaceutical packaging, medical device packaging boxes, etc., with high precision and stability, which can ensure the safety and stability of drugs.
Automotive parts packaging
For parts packaging in the automotive industry, such as protective packaging for interior and exterior parts, the positive and negative pressure three-station thermoforming blister machine can be personalized according to the shape of different parts to ensure efficient protection of packaging materials.
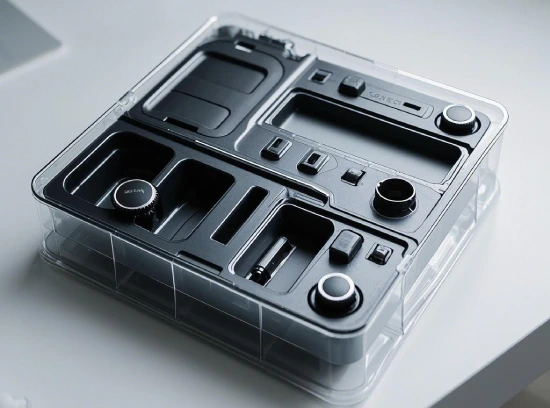
Thermoforming machine process flow
Heating
First, the plastic sheet is heated to a softened state and is ready to enter the forming mold. The heating temperature and time need to be precisely controlled to ensure that the plasticity of the sheet reaches the best state.
Forming
The heated plastic sheet is fed into the forming area. At this stage, the positive pressure pushes the sheet into the mold surface, while the negative pressure sucks the sheet into the groove of the mold to ensure its perfect forming.
Cooling
The plastic sheet remains in the mold for a certain period of time to cool and shape it. The cooling process ensures that the molded product has good dimensional accuracy and rigidity.
Demolding
After cooling and shaping, the molded plastic product is automatically demolded and removed, ready for the next step of processing or packaging.
Post-processing
In some applications, the molded product may require post-processing processes such as trimming, deburring, and printing to ensure that the final product meets customer needs.
Positive and negative pressure three-station thermoforming blister machine is widely used in packaging, electronics, food, medicine and other industries due to its high efficiency, precision and automation. It not only improves production efficiency and saves space, but also ensures high quality and consistency of products. With the improvement of environmental protection and energy saving requirements, this equipment also conforms to the development trend of modern industry and becomes one of the important equipment in the thermoforming industry.
Related Products
About SHENGAN
ShengAn (Shanghai) New Materials Co., Ltd – Your Trusted PET Sheet Solutions Provider
Established in 2018 in Shanghai, ShengAn specializes in high-quality PET sheets and thermoforming machinery, serving industries like electronics, food, cosmetics, and medical. With a 120,000 sqm facility and advanced production lines, we deliver over 10,000 metric tons annually, ensuring top-tier quality with ISO9001, GRS, and SGS certifications.
Key Offerings
- PET Sheets: APET, RPET (recycled), ESD Antistatic, GAG sheets.
- Machinery: Thermoforming, cup, and blister machines.
- Custom Solutions: OEM services tailored to your needs.
Global Reach
- Exporting to 70+ countries (Americas, Europe, Asia, Africa).
- Annual sales exceeding $10 million, with 71%-80% export volume.
Commitment to Excellence
- Customer-first approach: Comprehensive support and satisfaction guarantee.
- Sustainable practices: Eco-friendly materials and GRS-certified production.