Полная автоматическая крупная четырехэтажная термоформованная машина с положительным и отрицательным давлением
XG-A-3-3 High-Efficiency Programmable Plastic Pneumatic Thermoforming Machine, suitable for the forming of various plastic sheets such as HIPS, PLA, BOPS, PS, PP, PVC, PET, ABS, etc.
ЭнОбзор Quipment
Feature:
The XG-A-3-3 High-Efficiency Programmable Plastic Pneumatic Thermoforming Machine applies advanced plastic sheet forming technology and integrates machine, electricity, and air systems into one design. It utilizes a microcomputer and industrial control programmable PLC for operation, with an HMI (Human-Machine Interface) system.
The equipment includes a square tunnel-type imported radiation heater, capable of forming both male and female molds, and a laser blade cutting system. The process flow includes heating, forming, punching, cutting, stacking, and counting, which are all part of a multi-station production line.
The production line operates synchronously, employing the latest forming technology to reduce labor, prevent secondary contamination, save materials, improve product quality and compliance, significantly increase production efficiency, and enhance ease of operation, reliability, and functionality. It is an automated production line for sheet thermoforming and automatic punching and cutting of products.
Application:
Suitable for the forming of various plastic sheets such as HIPS, PLA, BOPS, PS, PP, PVC, PET, ABS, etc. The machine can produce high transparency, high stretch, shallow stretch, round, square, irregular, bi-directional stretching, flange, and other products. These include boxes, trays, bowls, lids, industrial packaging, electronic trays, food packaging, stationery packaging, cosmetic packaging, and other plastic packaging products.
ТЭхнические параметры
Term Description | Technical Parameters |
---|---|
Forming Mold Area | 850mm × 750mm |
Forming Mold Area | 350mm × 360mm |
Sheet Width | 800mm |
Sheet Width | 390mm |
Forming Height | Male mold: 130mm, Female mold: 120mm |
Толщина материала | 0.15—2,0 мм |
Forming Speed | 4-45 cycles/min (depending on product) |
Диаметр листа | 1000 мм (500 кг) |
Forming Mold Stroke | Upper: 150mm, Lower: 150mm |
Cutting Mold Stroke | Upper: 250mm, Lower: 150mm |
Punching Mold Stroke | 50 мм |
Cutting Mold Stroke | 50 мм |
Сила резки | 80 tons (for knife length ≤ 10 meters) |
Stacking System | 2.0kw and 1.5kw Delta servo motors from Taiwan, with stacking options for high products (<130mm) with hanging points to stack down, and low products (<80mm) with robotic arm either inside or outside the mold, 3 working modes available. |
Forming Station | Lower servo motor cam lever linkage with hard tooth gear reducer drive, upper servo motor cam lever linkage with hard tooth gear reducer drive. |
Cutting Station | Lower servo motor cam lever linkage with hard tooth gear reducer drive, upper servo motor cam lever linkage with hard tooth gear reducer direct punching. |
Метод охлаждения | High-pressure, large flow circulation water cooling for molds |
Client Air Source (external) | Поставка воздуха ≥ 5,5 мграни/мин, давление воздуха 0,6 ~ 0,8 МПа |
Power Supply | 380V/50HZ (Three-phase five-wire) |
Total Power | Installed power: 138KW (Normal operating power approx. 30-60KW) |
Total Weight (Reference) | 15.5T |
Dimensions | 14500 × 2000 × 3000mm (for reference) |
Мониторинг температуры пресс -формы | Temperature gauge to display actual mold temperature, ensuring product quality and production efficiency in real-time. |
Позиционирование стоимости | A. Integrated forming, cutting, and stacking system for smoother processing and lower energy consumption. B. Forming and cutting stations use sturdy mechanical structures with cam levers and roller bearings to ensure perfect forming and cutting. |
Метод формирования | Positive and negative pressure hot press thermoforming |
Cutting Station | Expandable mold table design, easy, safe, and quick mold replacement with laser cutting tool. |
ЭнПроцесс процесса Quipment
Sheet supply → Sheet transport → First heating stage → Second heating stage → Forming and cooling → Cutting → Separation and stacking → Waste material rewinding system
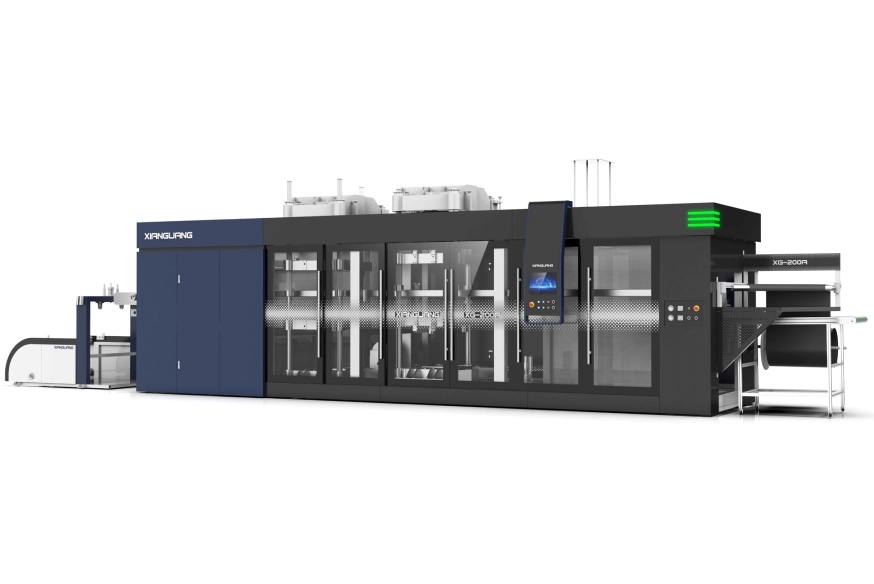
Note: The production line consists of three workstations. The operation mode can switch between manual and automatic, with manual operation facilitating sample extraction and parameter setting control.
ЭнТЕХНИЧЕСКОЕ ОПИСАНИЕ
A. Forming Equipment Structure:
The forming equipment consists of the main structural frame, positive and negative pressure forming system, temperature control system, vacuum system, heating system, pneumatic control system, electrical and PLC control system, punching system, product decomposing robotic arm stacking, and automatic waste material rewinding system.
B. Main Body Structure:
The main body is assembled from square tubes and channel steels, welded together to form the structure that supports heating, mold forming, mold punching, mold cutting, and auxiliary devices. The steel frame structure is designed following Structural Process Design, ensuring all involved parts meet the following standards: high-quality material selection, blank production methods, machining, heat treatment, part assembly, machine operation, and maintenance processes. This guarantees sufficient strength and rigidity for movable devices that transmit and convert motion and force. All metal surfaces are treated with anti-rust coating and base layer anti-corrosion paint. Standard components are used in the structure for easy maintenance and future part replacement.
C. Mold Table Structure:
The bottom servo motor cam lever linkage drives the hard tooth gear reducer, and the top servo motor cam lever linkage drives the same system.
D. Electrical and PLC Control System / Safety Features
Electrical Control System:
The electrical control system uses a PLC integrated module, with an industrial touch display as the HMI (Human-Machine Interface) featuring a Chinese interface. The machine includes button controls for operation and settings, as well as the ability to modify all process parameters, making it easy to operate and maintain.
Working Mode:
The machine operates in both manual and automatic modes. All settings and operations are handled via the touch display. After the operator places the material, pressing the “automatic” button starts the full process of thermoforming until the material in the hopper is processed. Manual mode is primarily used for mold changing or sample control.
Safety Measures:
The system includes multiple protection measures, with interlocking and closed-loop control to prevent collisions between moving parts.
The safety door is designed for manual locking and opening, and includes an integrated safety light curtain to enhance device safety, ensuring personnel and property safety.
Electrical Cabinet:
The electrical cabinet contains protective circuits, including overcurrent, overvoltage, undervoltage, short-circuit, and overload protection. The heating elements have fuse protection. For safety concerns that may pose a hazard to the system or parts, warning labels or notes are included. The control cabinet has 10% reserved space for future expansion of additional forming functions. The cabinet is equipped with filters and protective cooling fans.
Cables and Wiring:
All non-moving cables and wiring outside of power boxes are hidden in cable ducts, making it easier to access for repairs. If this is not possible, flexible hose fixation is used.
Emergency Stop Function:
Multiple “Аварийная остановка” buttons are installed at the front, middle, and rear of the equipment. The emergency stop button immediately cuts off the power supply, ensuring no dangerous situations arise during emergency stops.
Ведущийв восторге от продуктов
АБой Шенган
Shengan (Shanghai) New Materials Co., Ltd - ваш поставщик решений для домашних животных.
Основанный в 2018 году в Шанхае, Шенган специализируется на высококачественном Домашние листы и Термоформирование, Служба, такие как электроника, продукты питания, косметика и медицинская. Благодаря объекту площадью 120 000 кв. Сертификаты ISO9001, GRS и SGSПолем
Ключевые предложения
- Домашние листы: APET, RPET (переработанный), ESD антистатический, кляп.
- Машины: Термоформирование, чашка и блистерные машины.
- Пользовательские решения: Услуги OEM, адаптированные к вашим потребностям.
Глобальный охват
- Экспорт в 70+ стран (Америка, Европа, Азия, Африка).
- Годовые продажи превышают 10 миллионов долларов, с 71% -80% объемом экспорта.
Приверженность совершенству
- Первоначальный клиент подход: Комплексная гарантия поддержки и удовлетворения.
- Устойчивые практики: Экологичные материалы и сертифицированные GRS производство.